This article was originally written for CE-RISE and has been adapted for our blog with updates and additional insights.
The manufacturing industry is undergoing a significant transformation driven by the adoption of cutting-edge digital technologies. You may have come across the terms “Digital Product Passports” (DPPs) and “Digital Twins” — both are emerging as powerful tools that redefine how products are designed, produced, and managed throughout their lifecycle.
Both concepts involve the digital representation of physical objects and are often confused for the same thing. However, they are two different approaches to collecting, sharing, and processing data that complement each other.
In this article, we'll dive deep into the world of DPPs and digital twins, exploring their definitions and applications, how they differ, and how they can work together to unlock new sustainability opportunities. By the end, you will understand the nuanced roles these digital technologies have in shaping the future of sustainability and supply chain management.
What are digital product passports?
Digital product passports (DPPs) are digital files that contain comprehensive information about a product's environmental impact throughout its lifecycle.
First made mandatory in the EU's Ecodesign for Sustainable Products Regulation (ESPR), DPPs aim to enhance transparency and traceability in supply chains by providing detailed records of product origins, material compositions, and sustainability attributes.
Digital product passports allow stakeholders to share specific information with other actors within a value chain. But even for consumers who are not part of the value chain, companies can also offer general sustainability information and other public details, through digital product passports that are easily accessible via a website, as required by regulations.
Circular PU foam: An example of digital product passports in practice
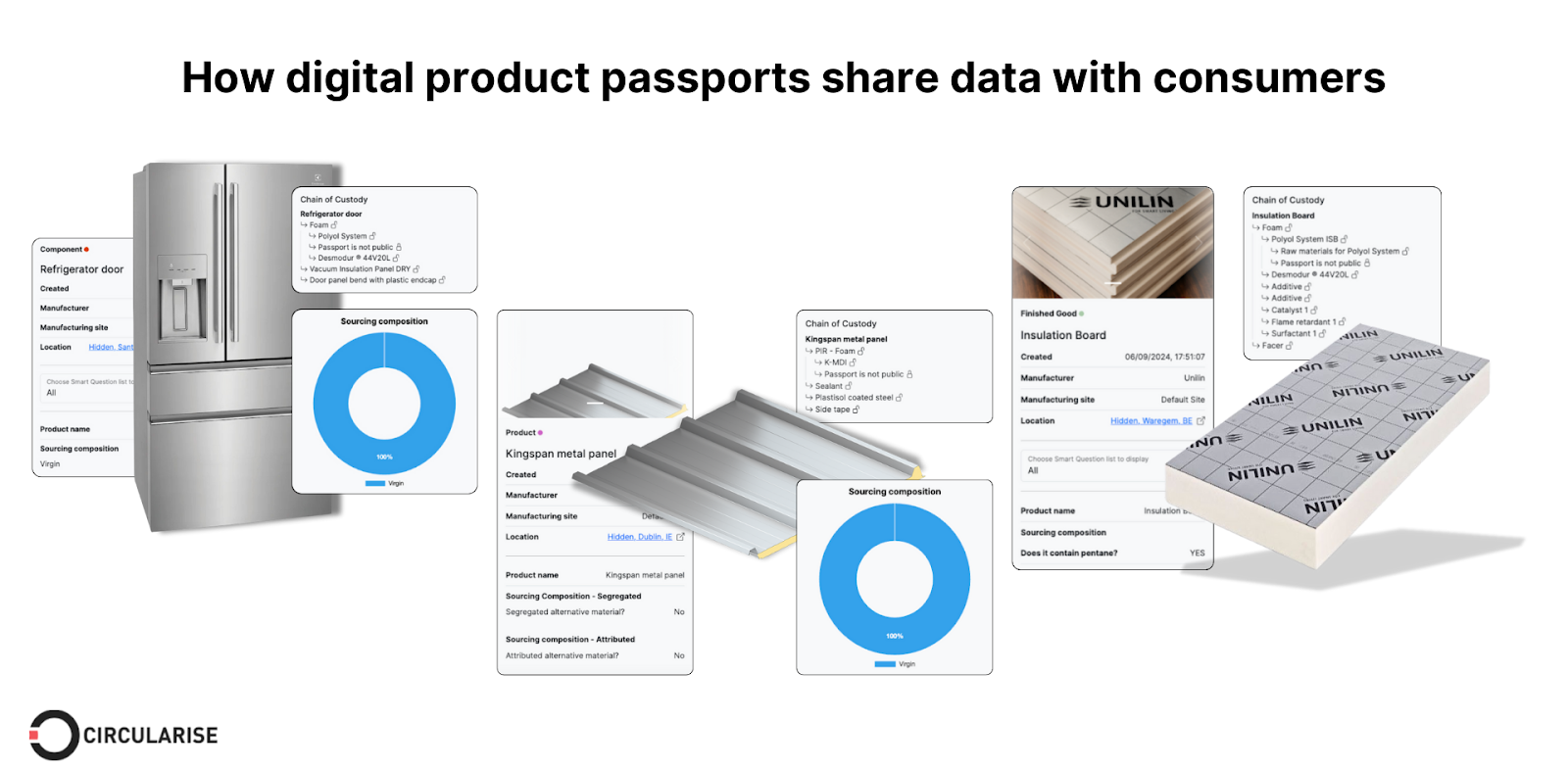
In the Circular Foam project, companies were able to achieve regulatory compliance while enhancing communication with customers via Circularise’s product traceability platform. Through this initiative, digital product passports (DPPs) were created for products containing recycled foam from Covestro — refrigerator doors by Electrolux, insulation boards by Unilin, and metal panels by Kingspan. These DPPs securely track each product’s lifecycle, offering sensitive information on chemical composition while safeguarding confidential data.
Other than providing information for the industrial partners, certain data was set up to give the DPP broader accessibility. This allows businesses to share key information such as sustainability metrics, regulatory compliance, and product dimensions with a wider audience. Consumers can access this data through web browsers or APIs, while end-of-life (EoL) stakeholders like recyclers use the data to make informed decisions about material reuse or recycling.
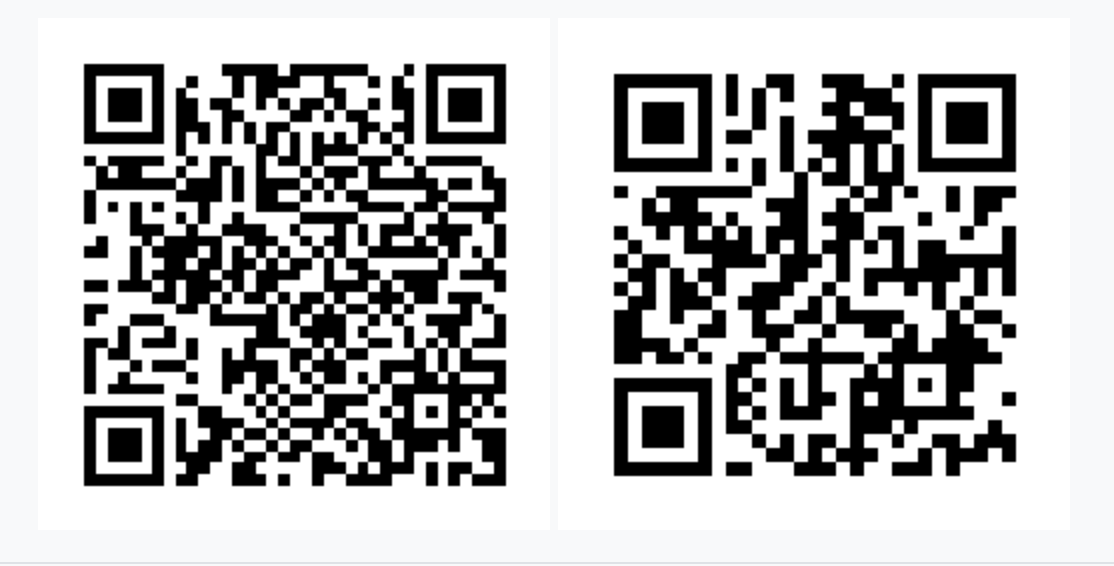
By allowing public and confidential data to coexist without compromising intellectual property, the Circular Foam project shows that Circularise’s DPPs can help advance circularity across industries. By enabling data sharing, manufacturers and stakeholders can make informed decisions for the environment, and consumers are empowered to make smarter choices in both purchasing and disposal.
What are digital twins?
Digital twins are virtual models that replicate physical objects, systems, or processes using real-time data and analytics to simulate real-world behaviour. They help optimise performance, predict maintenance needs, and enable data-driven decision-making.
Industries such as manufacturing, healthcare, and urban planning already leverage digital twins to improve efficiency, reduce operational disruptions, and optimise resource utilisation.
Sustainable aviation: An example of digital twin technology in practice
In the aerospace sector, Boeing’s use of digital twin technology helps them reduce waste, improve fuel consumption, and increase operational efficiency. Together with sensors placed on planes in operation, virtual replicas of physical aircraft simulate and monitor performance in real-time.
The data collected helps identify potential component issues before they impact the aircraft. This enables Boeing to predict maintenance needs, optimise fuel efficiency, and ensure the longevity of their aircraft. Integrated with Boeing’s maintenance systems, this wealth of data makes repairs and replacements more efficient, supporting longer, more sustainable aircraft lifecycles.1
Circularise is the leading software platform that provides end-to-end traceability for complex industrial supply chains. We offer two traceability solutions: MassBalancer to automate mass balance bookkeeping and Digital Product Passports for end-to-end batch traceability.